24小时服务电话:135-8585-8888
中文版
English
Language
搜索


新闻中心
News
如何通过动平衡机数据优化工件结构设计
- 分类:行业新闻
- 作者:DS视讯·(中国大陆)客户端编辑部
- 来源:上海DS视讯·(中国大陆)客户端动平衡机制造有限公司
- 发布时间:2025-04-17
- 访问量:11
通过动平衡机的数据优化工件结构设计是一个系统性的过程,需要结合测试数据、仿真分析和设计迭代。以下是具体的步骤和方法:
1. 数据采集与分析
- 获取关键数据:通过动平衡机测量工件的初始不平衡量(大小、相位角)、转速、振动幅值等,确定不平衡的轴向位置(校正平面)和偏心质量分布。
- 识别问题区域:根据不平衡量的分布,定位工件上质量过重或过轻的区域(如叶片根部、轴颈处等)。
- 频谱分析:结合振动频谱数据,判断不平衡是否由固有频率共振或其他动态问题引起。
2. 结构优化方向
(1) 质量分布调整
轻量化设计:在质量过大的区域(如轮毂、边缘)进行材料去除(钻孔、铣削),但需避免削弱结构强度。
对称性优化:通过调整几何形状(如叶片角度、厚度梯度)使质量分布更均匀。
配重设计:在允许的位置添加平衡块或调整现有配重的布局(需考虑可制造性)。
(2) 几何形状优化
流线型设计:减少气动/液动不平衡(如风机叶片采用变截面、扭曲设计)。
刚性与柔性平衡:通过加强筋或拓扑优化提高局部刚度,避免因变形导致动态失衡。
(3) 安装与连接优化
校正平面选择:优化动平衡校正平面的位置,使其更接近实际不平衡源。
接口设计:优化轴-轮毂连接方式(如过盈配合、键槽分布),避免装配偏差引入不平衡。
3. 仿真验证
- 有限元分析(FEA):模拟优化后的工件在旋转状态下的应力分布和变形,验证结构强度是否满足要求。
- 模态分析:检查优化后的固有频率是否远离工作转速,避免共振。
- 虚拟动平衡:通过仿真软件(如ANSYS、MSC Adams)预测不平衡量,验证设计改进效果。
4. 制造工艺优化
- 材料选择:采用密度更均匀的材料(如锻造件替代铸造件)。
- 加工精度控制:提高关键部位(如轴孔、叶片边缘)的加工精度,减少几何误差。
- 装配工艺改进:通过工装夹具确保零件对称安装,减少人为误差。
5. 迭代测试与反馈
- 制造优化后的样件,重新进行动平衡测试。
- 对比测试数据与仿真结果,确认优化效果。
- 若未达标,分析原因(如残余不平衡量、新引入的振动源),进一步调整设计。
6. 案例应用
- 风机叶片:通过动平衡数据调整叶片长度和厚度分布,使质心更接近旋转中心。
- 汽车曲轴:优化配重块形状和位置,减少高速旋转时的离心力不平衡。
- 电机转子:采用不对称槽设计或硅钢片叠压工艺,平衡电磁和机械质量分布。
注意事项
- 动态平衡与静态平衡的区别:高速旋转工件需同时满足动平衡(多平面校正)而非仅静平衡。
- 环境因素:考虑温度、转速变化对材料膨胀/收缩的影响。
- 成本与性能权衡:避免过度设计导致制造成本增加。 通过以上方法,动平衡机数据可转化为结构设计的关键输入,最终实现工件的高效、低振动、长寿命运行。
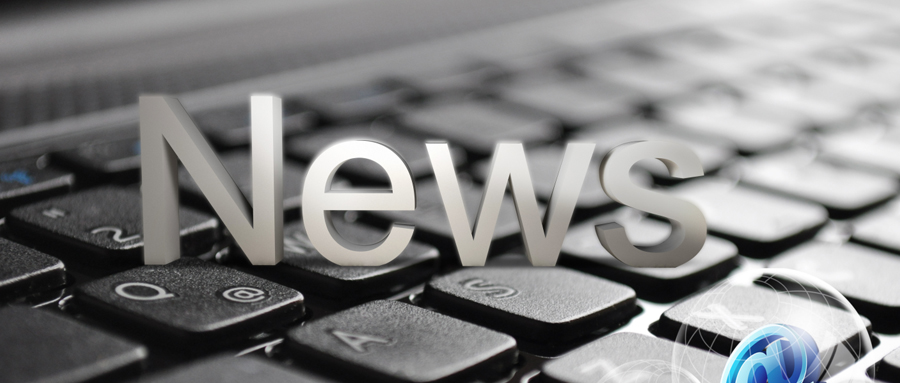
Copyright © 2003-2019 上海DS视讯·(中国大陆)客户端动平衡机制造有限公司, All Rights Reserved 沪ICP备16018888号-5 友情链接:
上海动平衡机