Copyright © 2003-2019 上海DS视讯·(中国大陆)客户端动平衡机制造有限公司, All Rights Reserved 沪ICP备16018888号-5 友情链接:
上海动平衡机
24小时服务电话:135-8585-8888
中文版
English
Language
搜索


新闻中心
News
精密机床主轴动平衡机加工的精度要求与工艺
- 分类:行业新闻
- 作者:DS视讯·(中国大陆)客户端编辑部
- 来源:上海DS视讯·(中国大陆)客户端动平衡机制造有限公司
- 发布时间:2025-04-15
- 访问量:3
精密机床主轴的动平衡加工是确保机床高速运转时振动小、精度高、寿命长的关键工艺。其精度要求与工艺控制涉及多个环节,以下从精度等级、工艺步骤及关键控制点进行详细说明:
一、动平衡精度要求
- 动平衡等级标准(ISO 1940-1)
- 典型等级:G0.4~G1.0(单位:mm/s),具体取决于主轴转速和应用场景。
- 半导体设备主轴:G0.4以下(超高精度)
- 精密磨床/加工中心:G0.6~G1.0
- 普通机床:G1.0~G2.5
- 计算公式:允许残余不平衡量 ( U = G imes (M imes 10^3) / (2pi n/60) )
- ( M ): 主轴质量(kg)
- ( n ): 工作转速(rpm)
- 典型等级:G0.4~G1.0(单位:mm/s),具体取决于主轴转速和应用场景。
- 具体参数要求
- 残余不平衡量:通常要求≤1g·mm/kg(主轴质量),高速主轴需≤0.5g·mm/kg。
- 振动速度:≤1.0mm/s(高频主轴可能需≤0.5mm/s)。
- 相位误差:≤5°(平衡配重的角度偏差)。
二、动平衡加工工艺流程
- 前期准备
- 主轴清洁:去除油污、碎屑,避免影响检测精度。
- 夹具设计:专用工装需保证重复定位精度≤0.005mm。
- 动平衡机校准:使用标准转子进行设备标定,确保传感器误差≤3%。
- 动平衡检测
- 测试转速:通常为工作转速的80%~120%,模拟实际工况。
- 传感器布置:双面平衡需在主轴两端安装振动传感器和相位探头。
- 数据采集:多次采样取平均值,消除随机误差。
- 不平衡修正
- 去重法(常用)
- 钻孔去重:深径比≤5:1,避免应力集中(如φ3mm孔,深度≤15mm)。
- 铣削/磨削:去除材料厚度≤0.2mm,表面粗糙度Ra≤1.6μm。
- 增重法(特殊场景)
- 配重块:铝合金/铜配重块,通过螺钉或胶粘固定,质量误差≤0.1g。
- 平衡环:可调式平衡环,调整角度精度±1°。
- 去重法(常用)
- 验证与迭代
- 复测平衡:修正后再次检测,直至残余不平衡量达标。
- 高温测试:针对高速主轴,在恒温箱内模拟热变形后的平衡状态。
三、工艺关键控制点
- 材料与结构优化
- 对称性设计:避免主轴结构不对称导致的初始不平衡。
- 材料均匀性:锻件需经过UT探伤,密度差≤0.5%。
- 热处理工艺:淬火后需进行去应力退火,防止变形。
- 加工细节控制
- 去重位置:优先选择非承载区(如法兰盘边缘),避免削弱刚性。
- 配重固定:螺钉需涂螺纹胶防松,胶粘配重要做剪切力测试(≥50N/mm?)。
- 表面处理:修正区域需做防锈处理(如镀镍或涂覆防腐层)。
- 环境与设备因素
- 温度控制:检测环境温度波动≤±2℃,避免热胀冷缩影响。
- 地基隔振:动平衡机需安装在独立地基或空气弹簧隔振平台上。
四、常见问题与解决
- 过度去重导致刚性下降
- 方案:改用增重法或优化去重位置,结合有限元分析验证应力分布。
- 平衡后主轴高速振动仍超标
- 原因:轴承预紧力不均或主轴自身弯曲。
- 措施:复测主轴径向跳动(要求≤2μm),调整轴承装配工艺。
- 配重块脱落
- 预防:胶粘配重需做48小时高温(80℃)老化测试,螺钉配重需扭矩校验。
五、应用案例
- 案例1:某5轴加工中心主轴(转速18,000rpm)
- 工艺:双面动平衡,G0.8等级,钻孔去重(φ2mm×8mm,共3孔)。
- 结果:振动从2.5mm/s降至0.7mm/s,刀具寿命提升30%。
- 案例2:半导体晶圆切割主轴(40,000rpm)
- 工艺:增重法(钨合金配重块),平衡后残余量0.3g·mm/kg。
- 关键点:真空环境下检测,避免空气扰动影响。
总结
精密主轴动平衡需结合理论计算、高精度设备及工艺经验,重点关注材料均匀性、修正方法合理性及环境稳定性。对于超高速主轴(>50,000rpm),还需考虑空气动力学效应和转子动力学特性,采用在线动平衡技术实时校正。
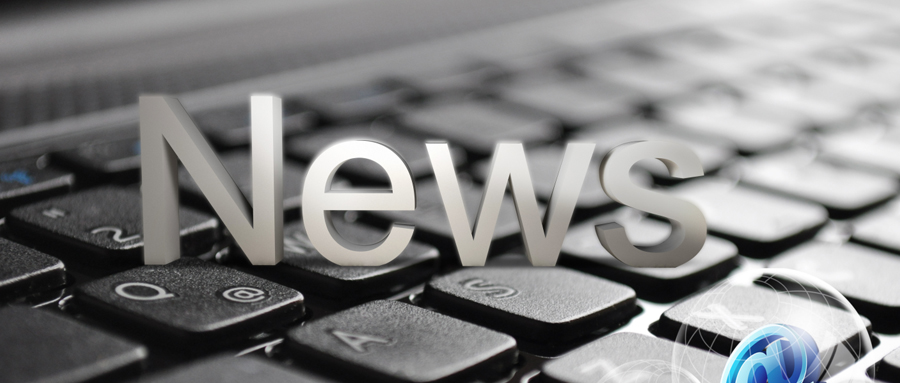