24小时服务电话:135-8585-8888
中文版
English
Language
搜索


新闻中心
News
如何通过动平衡机数据分析找出加工瓶颈环节
- 分类:行业新闻
- 作者:DS视讯·(中国大陆)客户端编辑部
- 来源:上海DS视讯·(中国大陆)客户端动平衡机制造有限公司
- 发布时间:2025-04-17
- 访问量:5
通过动平衡机数据分析识别加工瓶颈环节,需要系统性地收集、分析和关联数据,结合工艺知识定位问题根源。以下是具体步骤和方法:
1. 数据收集与整理
- 关键数据项:
- 不平衡量数据:初始不平衡量(校正前)、残余不平衡量(校正后)、相位角度分布。
- 工艺参数:加工转速、刀具类型、切削参数(进给量、切削深度)、材料批次。
- 设备状态:机床振动幅值、夹具精度、传感器校准记录。
- 过程数据:校正操作耗时、校正次数、返工率。
- 数据预处理:
- 按加工工序(如粗加工、精加工、装配、校正)分类数据。
- 剔除异常值(如传感器故障导致的离群数据)。
2. 数据分析方法
#### (1) 统计分布分析
直方图对比:对比各工序(如车削、磨削、钻孔)后的工件初始不平衡量分布。
- 若某一工序后的不平衡量标准差显著增大,表明该环节一致性差(如刀具磨损或夹具松动)。
过程能力指数(Cpk):计算各工序的Cpk值,识别能力不足的环节(Cpk <1.33即需改进)。
(2) 趋势分析
时间序列分析:观察不平衡量随时间的变化趋势。
- 例如:若精磨工序后的残余不平衡量随刀具使用时间逐步上升,表明刀具寿命管理存在问题。
批次相关性:分析不同材料批次的不平衡量差异,排查原材料均匀性问题。
(3) 相位角度诊断
相位集中性:若不平衡量的相位角度在某一工序后集中在特定区域(如90°~180°),可能指示加工方向性偏差(如铣削受力不均)。
相位偏移分析:校正前后的相位偏移量过大,可能反映夹具定位误差或动平衡算法缺陷。
(4) 相关性分析
多变量回归:建立不平衡量与工艺参数(如转速、进给速度)的数学模型,识别关键影响因子。
热力图(Heatmap):可视化不同参数组合(如“转速+切削深度”)下的不平衡量分布,找出高风险参数区间。
3. 瓶颈环节定位
- 材料阶段瓶颈:
- 若初始不平衡量(未校正)普遍偏高且与材料批次强相关,需加强原材料密度检测或供应商管理。
- 加工阶段瓶颈:
- 机床问题:如主轴径向跳动超差导致重复加工误差,可通过振动频谱分析验证。
- 刀具/工艺问题:若某工序后不平衡量分布呈多峰形态,可能因刀具崩刃或切削参数不合理。
- 装配阶段瓶颈:
- 若装配后不平衡量突变(如联轴器不同轴),需检查配合公差或螺栓预紧力。
- 校正阶段瓶颈:
- 若校正后残余不平衡量仍超差,需验证校正算法权重设置或执行机构(如去重钻头)精度。
4. 验证与优化
- 根本原因验证:
- 替换法:更换怀疑环节的刀具/夹具后,观察数据是否改善。
- 实验设计(DOE):调整关键参数(如降低切削速度)并验证对不平衡量的影响。
- 优化措施:
- 工艺改进:优化切削参数、增加半精加工工序。
- 设备维护:定期校准传感器、加强主轴动态平衡。
- 智能化校正:采用自适应校正算法(如基于机器学习的权重预测)。
5. 持续监控
- 实时监控看板:在动平衡机系统中集成SPC(统计过程控制)看板,实时报警异常工序。
- 闭环反馈:将分析结果反馈至MES(制造执行系统),自动触发工艺参数调整或维护工单。
示例场景
假设某电机转子加工中,动平衡数据显示:
- 精车工序后:初始不平衡量均值为30g·mm,标准差为5g·mm;
- 磨削工序后:均值升至50g·mm,标准差达15g·mm;
- 校正后:残余不平衡量仍超差(目标值<10g·mm)。 分析结论:
- 磨削工序是瓶颈,可能因砂轮动平衡不良或进给速度过快导致表面振纹。
- 优化方案:降低磨削进给速度20%,并增加砂轮动态平衡校准频率。
通过上述方法,可系统性地将动平衡数据转化为工艺改进洞察,精准定位并消除瓶颈环节。
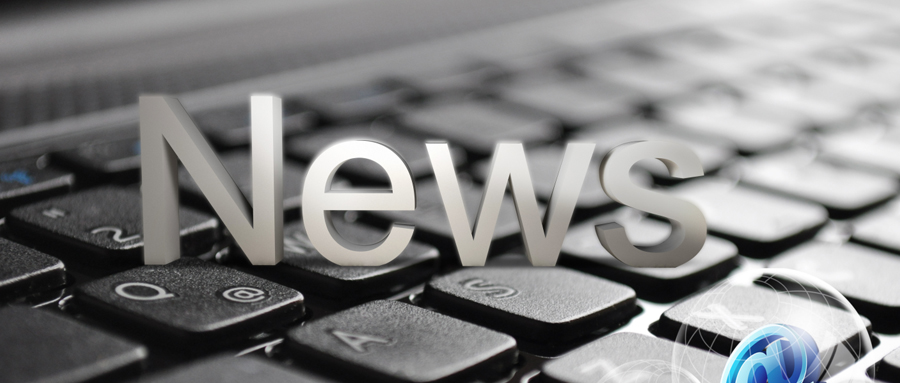
Copyright © 2003-2019 上海DS视讯·(中国大陆)客户端动平衡机制造有限公司, All Rights Reserved 沪ICP备16018888号-5 友情链接:
上海动平衡机